Why complex landing gears are used instead of simple,reliability and light weight muscle wire or shape memory...
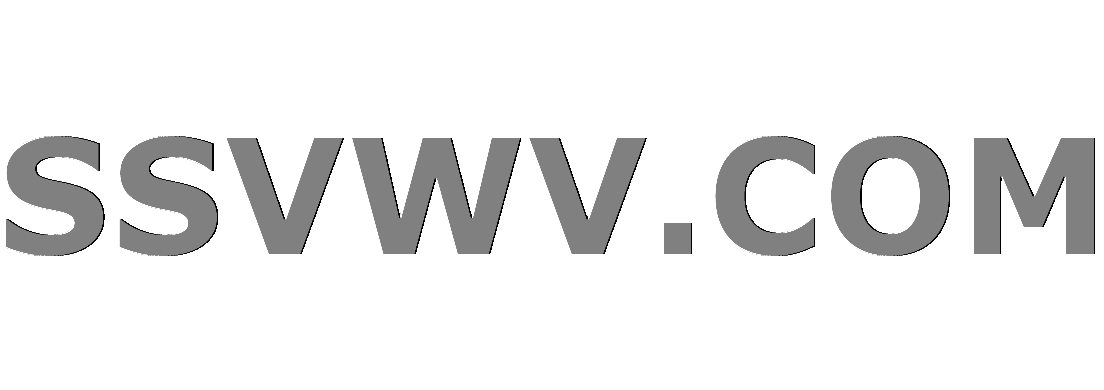
Multi tool use
How were pictures turned from film to a big picture in a picture frame before digital scanning?
AppleTVs create a chatty alternate WiFi network
Why is the change of basis formula counter-intuitive? [See details]
I can't produce songs
How can a team of shapeshifters communicate?
Is openssl rand command cryptographically secure?
One-one communication
Printing attributes of selection in ArcPy?
What does 丫 mean? 丫是什么意思?
Resize vertical bars (absolute-value symbols)
If Windows 7 doesn't support WSL, then what is "Subsystem for UNIX-based Applications"?
Why is std::move not [[nodiscard]] in C++20?
What is a more techy Technical Writer job title that isn't cutesy or confusing?
I got rid of Mac OSX and replaced it with linux but now I can't change it back to OSX or windows
Putting class ranking in CV, but against dept guidelines
After Sam didn't return home in the end, were he and Al still friends?
How to change the tick of the color bar legend to black
What does the writing on Poe's helmet say?
Does silver oxide react with hydrogen sulfide?
Most effective melee weapons for arboreal combat? (pre-gunpowder technology)
Caught masturbating at work
How can god fight other gods?
Where is the Next Backup Size entry on iOS 12?
How to ask rejected full-time candidates to apply to teach individual courses?
Why complex landing gears are used instead of simple,reliability and light weight muscle wire or shape memory alloys?
Announcing the arrival of Valued Associate #679: Cesar Manara
Planned maintenance scheduled April 23, 2019 at 23:30 UTC (7:30pm US/Eastern)Why safe take off weight exceeds the safe landing weight?Why does the Harrier jet have four landing gears?Is there a good reason why modern airliners can't have conventional landing gears (vs. tricycle landing gears)?Is it feasible to replace brakes on airplanes with electric motor/generator?Why are there so many moving parts used in the landing gear?Why do some A320s have double bogey landing gears?Why are aircraft tires not pre-spun prior to landing?Why do landing gears smoke upon impact?Why was the cabin light turned off before landing?Why don't nose landing gears have brakes?
$begingroup$
Muscle wires actuators are really simple, high power density and reliable. Landing gears on other hand are used only twice per flight while taking off and landing (if everything goes well though). During flight these machines are not useful and there are number of gear up landing because of landing gear failure.
What is so complex in landing gear?
Why electric motors/ hydraulic actuators are used instead of muscle wire actuators in landing gear which are simple, light weight, reliable and cheap?
(If it is electric power requirements, that can be achieved by supercapacitors.)
aircraft-design landing landing-gear
New contributor
SRD is a new contributor to this site. Take care in asking for clarification, commenting, and answering.
Check out our Code of Conduct.
$endgroup$
add a comment |
$begingroup$
Muscle wires actuators are really simple, high power density and reliable. Landing gears on other hand are used only twice per flight while taking off and landing (if everything goes well though). During flight these machines are not useful and there are number of gear up landing because of landing gear failure.
What is so complex in landing gear?
Why electric motors/ hydraulic actuators are used instead of muscle wire actuators in landing gear which are simple, light weight, reliable and cheap?
(If it is electric power requirements, that can be achieved by supercapacitors.)
aircraft-design landing landing-gear
New contributor
SRD is a new contributor to this site. Take care in asking for clarification, commenting, and answering.
Check out our Code of Conduct.
$endgroup$
$begingroup$
You may provide some links or reading about muscle wire actuator as I'm not sure how familiar is the aviation.SE community with this kind of actuator and how it is operated. Moreover, you may restrict your question to one kind of aircraft as many GA aircrafts are equipped with fixed landing gear
$endgroup$
– Manu H
8 hours ago
add a comment |
$begingroup$
Muscle wires actuators are really simple, high power density and reliable. Landing gears on other hand are used only twice per flight while taking off and landing (if everything goes well though). During flight these machines are not useful and there are number of gear up landing because of landing gear failure.
What is so complex in landing gear?
Why electric motors/ hydraulic actuators are used instead of muscle wire actuators in landing gear which are simple, light weight, reliable and cheap?
(If it is electric power requirements, that can be achieved by supercapacitors.)
aircraft-design landing landing-gear
New contributor
SRD is a new contributor to this site. Take care in asking for clarification, commenting, and answering.
Check out our Code of Conduct.
$endgroup$
Muscle wires actuators are really simple, high power density and reliable. Landing gears on other hand are used only twice per flight while taking off and landing (if everything goes well though). During flight these machines are not useful and there are number of gear up landing because of landing gear failure.
What is so complex in landing gear?
Why electric motors/ hydraulic actuators are used instead of muscle wire actuators in landing gear which are simple, light weight, reliable and cheap?
(If it is electric power requirements, that can be achieved by supercapacitors.)
aircraft-design landing landing-gear
aircraft-design landing landing-gear
New contributor
SRD is a new contributor to this site. Take care in asking for clarification, commenting, and answering.
Check out our Code of Conduct.
New contributor
SRD is a new contributor to this site. Take care in asking for clarification, commenting, and answering.
Check out our Code of Conduct.
edited 8 hours ago
SRD
New contributor
SRD is a new contributor to this site. Take care in asking for clarification, commenting, and answering.
Check out our Code of Conduct.
asked 9 hours ago
SRDSRD
343
343
New contributor
SRD is a new contributor to this site. Take care in asking for clarification, commenting, and answering.
Check out our Code of Conduct.
New contributor
SRD is a new contributor to this site. Take care in asking for clarification, commenting, and answering.
Check out our Code of Conduct.
SRD is a new contributor to this site. Take care in asking for clarification, commenting, and answering.
Check out our Code of Conduct.
$begingroup$
You may provide some links or reading about muscle wire actuator as I'm not sure how familiar is the aviation.SE community with this kind of actuator and how it is operated. Moreover, you may restrict your question to one kind of aircraft as many GA aircrafts are equipped with fixed landing gear
$endgroup$
– Manu H
8 hours ago
add a comment |
$begingroup$
You may provide some links or reading about muscle wire actuator as I'm not sure how familiar is the aviation.SE community with this kind of actuator and how it is operated. Moreover, you may restrict your question to one kind of aircraft as many GA aircrafts are equipped with fixed landing gear
$endgroup$
– Manu H
8 hours ago
$begingroup$
You may provide some links or reading about muscle wire actuator as I'm not sure how familiar is the aviation.SE community with this kind of actuator and how it is operated. Moreover, you may restrict your question to one kind of aircraft as many GA aircrafts are equipped with fixed landing gear
$endgroup$
– Manu H
8 hours ago
$begingroup$
You may provide some links or reading about muscle wire actuator as I'm not sure how familiar is the aviation.SE community with this kind of actuator and how it is operated. Moreover, you may restrict your question to one kind of aircraft as many GA aircrafts are equipped with fixed landing gear
$endgroup$
– Manu H
8 hours ago
add a comment |
1 Answer
1
active
oldest
votes
$begingroup$
Shape-memory alloys change their shape with temperature, with control usually achieved with electric heating in one direction, and back with convective heat transfer to the environment. There is one specific temperature where the change in shape occurs. There are two huge problems with this:
The operating temperature range for gear actuators is huge. It may easily be below -40°C on a cold arctic night, but on a hot tropical day the sun can easily heat the structure to upward of +60°C. That means the transformation temperature must be pretty high, but that means a lot of energy has to be put to heating it, especially if the ambient temperature happens to be low on the day.
Note that the actuators are not very energy efficient. A super-capacitor can give you high peak power if you need that, but will not help at all with the total energy. The work the actuator has to do is significant, so the efficiency matters.
Worse, a shape-memory alloy actuator requires constant power to remain at one end of the motion range and spontaneously returns to the other. However, gear must be stable in both end positions without requiring energy, so there would still have to be uplocks and separate actuator for extension or retraction (or maybe extension would be gravity-only, but then you have to ensure it gets reliably locked). Not really simple anymore.
I also don't think they actually scale to the required forces and displacements well. A 2 mm wire bends quite easily, 2 cm rod, not so much. The thicker will of course need more force to bend—which is OK—but it will also break much sooner, because the difference in strain is bigger.
$endgroup$
add a comment |
Your Answer
StackExchange.ready(function() {
var channelOptions = {
tags: "".split(" "),
id: "528"
};
initTagRenderer("".split(" "), "".split(" "), channelOptions);
StackExchange.using("externalEditor", function() {
// Have to fire editor after snippets, if snippets enabled
if (StackExchange.settings.snippets.snippetsEnabled) {
StackExchange.using("snippets", function() {
createEditor();
});
}
else {
createEditor();
}
});
function createEditor() {
StackExchange.prepareEditor({
heartbeatType: 'answer',
autoActivateHeartbeat: false,
convertImagesToLinks: false,
noModals: true,
showLowRepImageUploadWarning: true,
reputationToPostImages: null,
bindNavPrevention: true,
postfix: "",
imageUploader: {
brandingHtml: "Powered by u003ca class="icon-imgur-white" href="https://imgur.com/"u003eu003c/au003e",
contentPolicyHtml: "User contributions licensed under u003ca href="https://creativecommons.org/licenses/by-sa/3.0/"u003ecc by-sa 3.0 with attribution requiredu003c/au003e u003ca href="https://stackoverflow.com/legal/content-policy"u003e(content policy)u003c/au003e",
allowUrls: true
},
noCode: true, onDemand: true,
discardSelector: ".discard-answer"
,immediatelyShowMarkdownHelp:true
});
}
});
SRD is a new contributor. Be nice, and check out our Code of Conduct.
Sign up or log in
StackExchange.ready(function () {
StackExchange.helpers.onClickDraftSave('#login-link');
});
Sign up using Google
Sign up using Facebook
Sign up using Email and Password
Post as a guest
Required, but never shown
StackExchange.ready(
function () {
StackExchange.openid.initPostLogin('.new-post-login', 'https%3a%2f%2faviation.stackexchange.com%2fquestions%2f62546%2fwhy-complex-landing-gears-are-used-instead-of-simple-reliability-and-light-weigh%23new-answer', 'question_page');
}
);
Post as a guest
Required, but never shown
1 Answer
1
active
oldest
votes
1 Answer
1
active
oldest
votes
active
oldest
votes
active
oldest
votes
$begingroup$
Shape-memory alloys change their shape with temperature, with control usually achieved with electric heating in one direction, and back with convective heat transfer to the environment. There is one specific temperature where the change in shape occurs. There are two huge problems with this:
The operating temperature range for gear actuators is huge. It may easily be below -40°C on a cold arctic night, but on a hot tropical day the sun can easily heat the structure to upward of +60°C. That means the transformation temperature must be pretty high, but that means a lot of energy has to be put to heating it, especially if the ambient temperature happens to be low on the day.
Note that the actuators are not very energy efficient. A super-capacitor can give you high peak power if you need that, but will not help at all with the total energy. The work the actuator has to do is significant, so the efficiency matters.
Worse, a shape-memory alloy actuator requires constant power to remain at one end of the motion range and spontaneously returns to the other. However, gear must be stable in both end positions without requiring energy, so there would still have to be uplocks and separate actuator for extension or retraction (or maybe extension would be gravity-only, but then you have to ensure it gets reliably locked). Not really simple anymore.
I also don't think they actually scale to the required forces and displacements well. A 2 mm wire bends quite easily, 2 cm rod, not so much. The thicker will of course need more force to bend—which is OK—but it will also break much sooner, because the difference in strain is bigger.
$endgroup$
add a comment |
$begingroup$
Shape-memory alloys change their shape with temperature, with control usually achieved with electric heating in one direction, and back with convective heat transfer to the environment. There is one specific temperature where the change in shape occurs. There are two huge problems with this:
The operating temperature range for gear actuators is huge. It may easily be below -40°C on a cold arctic night, but on a hot tropical day the sun can easily heat the structure to upward of +60°C. That means the transformation temperature must be pretty high, but that means a lot of energy has to be put to heating it, especially if the ambient temperature happens to be low on the day.
Note that the actuators are not very energy efficient. A super-capacitor can give you high peak power if you need that, but will not help at all with the total energy. The work the actuator has to do is significant, so the efficiency matters.
Worse, a shape-memory alloy actuator requires constant power to remain at one end of the motion range and spontaneously returns to the other. However, gear must be stable in both end positions without requiring energy, so there would still have to be uplocks and separate actuator for extension or retraction (or maybe extension would be gravity-only, but then you have to ensure it gets reliably locked). Not really simple anymore.
I also don't think they actually scale to the required forces and displacements well. A 2 mm wire bends quite easily, 2 cm rod, not so much. The thicker will of course need more force to bend—which is OK—but it will also break much sooner, because the difference in strain is bigger.
$endgroup$
add a comment |
$begingroup$
Shape-memory alloys change their shape with temperature, with control usually achieved with electric heating in one direction, and back with convective heat transfer to the environment. There is one specific temperature where the change in shape occurs. There are two huge problems with this:
The operating temperature range for gear actuators is huge. It may easily be below -40°C on a cold arctic night, but on a hot tropical day the sun can easily heat the structure to upward of +60°C. That means the transformation temperature must be pretty high, but that means a lot of energy has to be put to heating it, especially if the ambient temperature happens to be low on the day.
Note that the actuators are not very energy efficient. A super-capacitor can give you high peak power if you need that, but will not help at all with the total energy. The work the actuator has to do is significant, so the efficiency matters.
Worse, a shape-memory alloy actuator requires constant power to remain at one end of the motion range and spontaneously returns to the other. However, gear must be stable in both end positions without requiring energy, so there would still have to be uplocks and separate actuator for extension or retraction (or maybe extension would be gravity-only, but then you have to ensure it gets reliably locked). Not really simple anymore.
I also don't think they actually scale to the required forces and displacements well. A 2 mm wire bends quite easily, 2 cm rod, not so much. The thicker will of course need more force to bend—which is OK—but it will also break much sooner, because the difference in strain is bigger.
$endgroup$
Shape-memory alloys change their shape with temperature, with control usually achieved with electric heating in one direction, and back with convective heat transfer to the environment. There is one specific temperature where the change in shape occurs. There are two huge problems with this:
The operating temperature range for gear actuators is huge. It may easily be below -40°C on a cold arctic night, but on a hot tropical day the sun can easily heat the structure to upward of +60°C. That means the transformation temperature must be pretty high, but that means a lot of energy has to be put to heating it, especially if the ambient temperature happens to be low on the day.
Note that the actuators are not very energy efficient. A super-capacitor can give you high peak power if you need that, but will not help at all with the total energy. The work the actuator has to do is significant, so the efficiency matters.
Worse, a shape-memory alloy actuator requires constant power to remain at one end of the motion range and spontaneously returns to the other. However, gear must be stable in both end positions without requiring energy, so there would still have to be uplocks and separate actuator for extension or retraction (or maybe extension would be gravity-only, but then you have to ensure it gets reliably locked). Not really simple anymore.
I also don't think they actually scale to the required forces and displacements well. A 2 mm wire bends quite easily, 2 cm rod, not so much. The thicker will of course need more force to bend—which is OK—but it will also break much sooner, because the difference in strain is bigger.
edited 8 hours ago
answered 8 hours ago
Jan HudecJan Hudec
40.8k4107197
40.8k4107197
add a comment |
add a comment |
SRD is a new contributor. Be nice, and check out our Code of Conduct.
SRD is a new contributor. Be nice, and check out our Code of Conduct.
SRD is a new contributor. Be nice, and check out our Code of Conduct.
SRD is a new contributor. Be nice, and check out our Code of Conduct.
Thanks for contributing an answer to Aviation Stack Exchange!
- Please be sure to answer the question. Provide details and share your research!
But avoid …
- Asking for help, clarification, or responding to other answers.
- Making statements based on opinion; back them up with references or personal experience.
Use MathJax to format equations. MathJax reference.
To learn more, see our tips on writing great answers.
Sign up or log in
StackExchange.ready(function () {
StackExchange.helpers.onClickDraftSave('#login-link');
});
Sign up using Google
Sign up using Facebook
Sign up using Email and Password
Post as a guest
Required, but never shown
StackExchange.ready(
function () {
StackExchange.openid.initPostLogin('.new-post-login', 'https%3a%2f%2faviation.stackexchange.com%2fquestions%2f62546%2fwhy-complex-landing-gears-are-used-instead-of-simple-reliability-and-light-weigh%23new-answer', 'question_page');
}
);
Post as a guest
Required, but never shown
Sign up or log in
StackExchange.ready(function () {
StackExchange.helpers.onClickDraftSave('#login-link');
});
Sign up using Google
Sign up using Facebook
Sign up using Email and Password
Post as a guest
Required, but never shown
Sign up or log in
StackExchange.ready(function () {
StackExchange.helpers.onClickDraftSave('#login-link');
});
Sign up using Google
Sign up using Facebook
Sign up using Email and Password
Post as a guest
Required, but never shown
Sign up or log in
StackExchange.ready(function () {
StackExchange.helpers.onClickDraftSave('#login-link');
});
Sign up using Google
Sign up using Facebook
Sign up using Email and Password
Sign up using Google
Sign up using Facebook
Sign up using Email and Password
Post as a guest
Required, but never shown
Required, but never shown
Required, but never shown
Required, but never shown
Required, but never shown
Required, but never shown
Required, but never shown
Required, but never shown
Required, but never shown
EK5nqe6p
$begingroup$
You may provide some links or reading about muscle wire actuator as I'm not sure how familiar is the aviation.SE community with this kind of actuator and how it is operated. Moreover, you may restrict your question to one kind of aircraft as many GA aircrafts are equipped with fixed landing gear
$endgroup$
– Manu H
8 hours ago